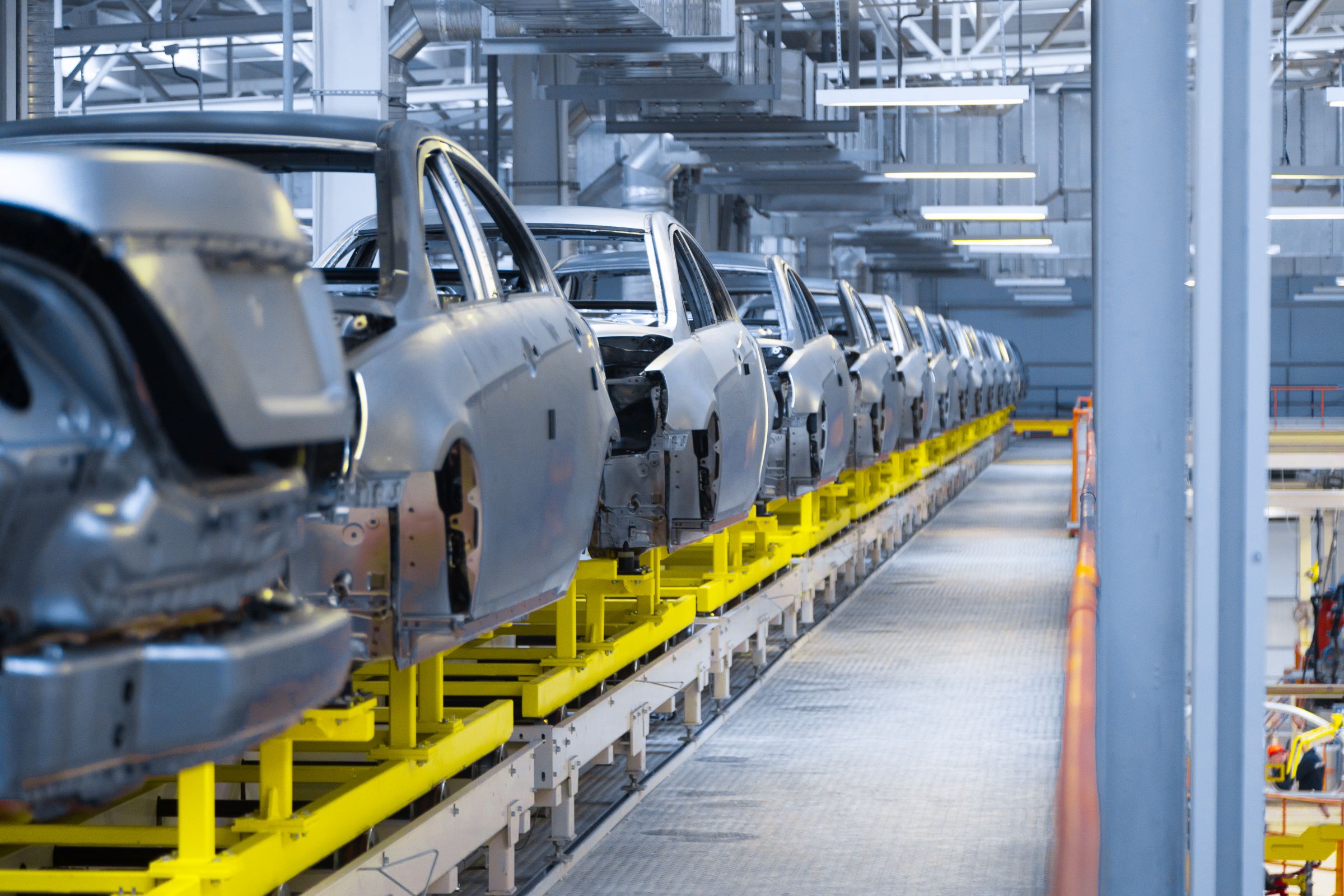
PPAP & IMDS
PPAP (Production Part Approval Process) is a well-known automotive industry standard that ensures the components produced by suppliers meet the requirements of automotive manufacturers. In this article, we will explore the history, purpose, and process of PPAP.
IMDS (International Material Data System) is a tool used to manage and report material information, particularly in the automotive and other industrial sectors. The following will briefly introduce how PPAP and IMDS can help companies meet environmental and sustainability requirements.
PPAP (Production Part Approval Process)
PPAP determines the approval process for new or revised components, or components produced from significantly new production methods. The documentation was introduced by AIAG (Automotive Industry Action Group), that requires 18 elements:
1) Design Records of Saleable Product
2) Engineering Change Documents, if any
3) Customer Engineering approval, if required
4) Design FMEA
5) Process Flow Diagrams
6) Process FMEA
7) Dimensional Results
8) Material, Performance Test Results
9) Initial Process Study
10) Measurement System Analysis Studies
11) Qualified Laboratory Documentation
12) Control Plan
13) Part Submission Warrant (PSW)
14) Appearance Approval Report (AAR), if applicable
15) Bulk Material Requirements Checklist (for bulk material PPAP only)
16) Sample Product
17) Master Sample
18) Checking Aids
IMDS Registration
IMDS (International Material Data System) is a system that gathers mostly material data from automotive industry. The system was initially created by Audi, BMW, Daimler, DXC, Ford, Opel, Porsche, VW and Volvo, in order to conform ELV, CPSIA and HF regulations. All materials and components applied to automobile should be collected, maintained, analyzed and archived. The community aims to pursue sustainable development and environmental friendly, therefore most automakers have participated the IMDS. In recent years, electronics industry has joined IMDS as well.