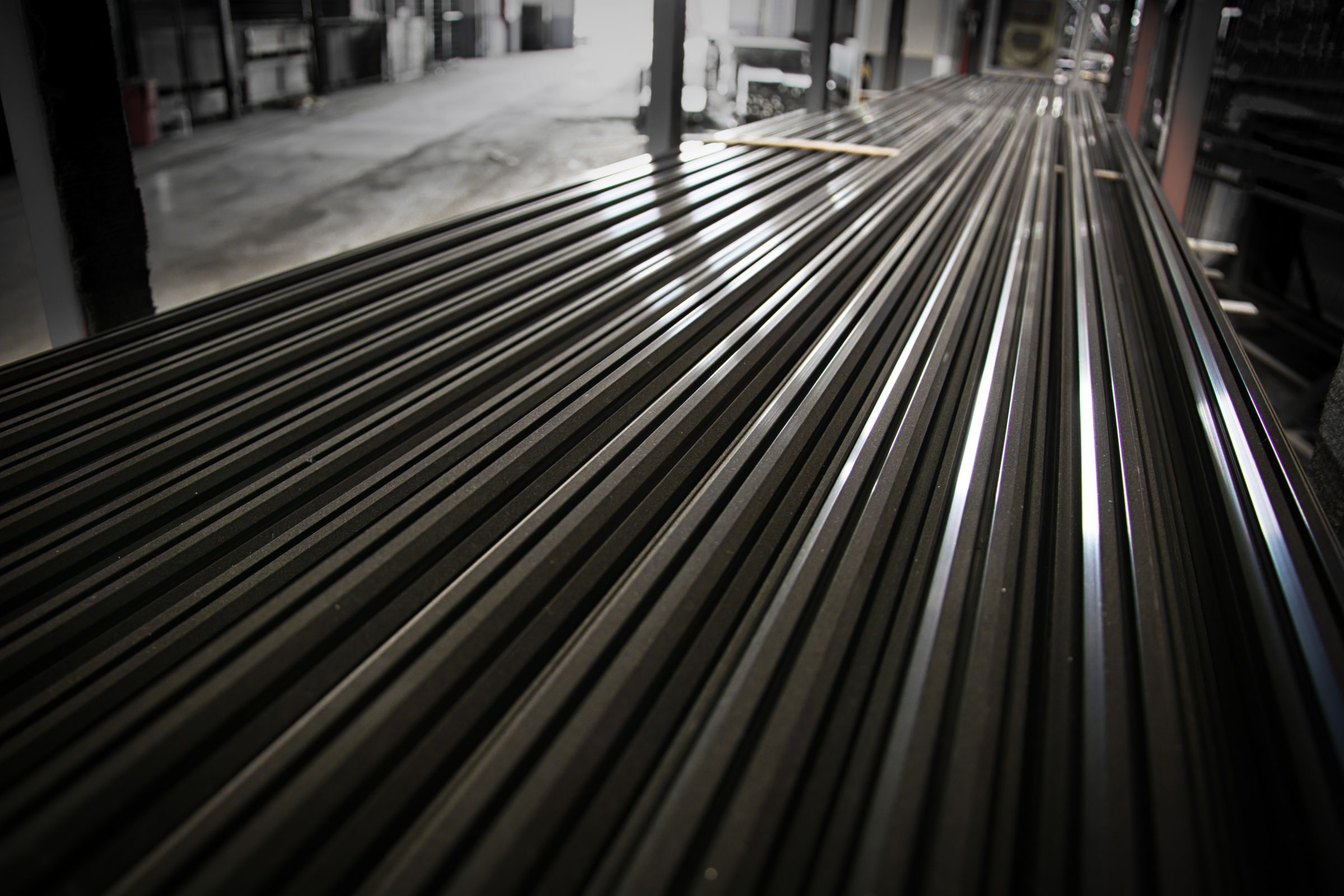
Finish of stainless steel components: Passivation
Passivation process is a chemical film that formed when stainless steel parts are exposed to an oxygen environment. Formation of this passivation film will be damaged by contaminants (dirt, oil, grease) and free iron on surface of the part. Therefore a special passivation process is designed to remove these impurities.
■ Standard
ASTM standards A380 and A967 provide guidelines for good passivation practices toward many types of parts and industries. These standards detail acceptable methods for passivation of stainless steel and provide tests to measure the success rate of passivation.
■ Process
Cleaning is the first step in the passivation process. The required cleaning type depends on the contaminants and shape of the part. Cleaner should be suitable for the type of soil to be removed and should be handled in accordance with safety and environmental regulations.
■ Selection of Acid
The purpose of this step is to remove free iron and contaminants that may remain after the last steps and to enhance corrosion resistance. Nitric acid has always been the traditional acid of choice for this passivation step, although both ASTM A967 and AMS2700C allow the use of citric acid. Citric acid is more friendly than nitric acid in terms of safety and environment, so citric acid has been developed.
■ Rinse
Perform one or more rinsing immediately after the passivation bath. The rinsed part should be dried quickly.
■ Finish
After passivation, rinsing and drying are completed, parts should be free of any surface defects or stains of free iron.